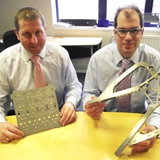
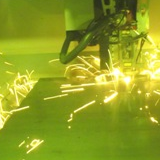
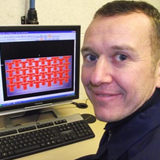
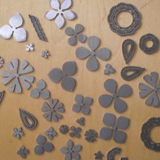
RADAN Nesting Role Helps Keep Altex Dynamic
Nesting capabilities of the world’s most powerful sheet metal CAD/CAM software, RADAN, proved so vital for Altex Engineering Ltd that they have created a new role for a shop floor worker dealing almost exclusively with nests.
Martin Brewer (pictured right) now controls all nesting for the sheet metal subcontractor on their Salvagnini fibre laser and LVD punch press.
“Due to the nature of the subcontract industry our priorities change on a daily basis,” says Managing Director Adrian Brewer (no relation to Martin). “It’s Martin’s job to produce the best RADAN nests for that particular moment and use as little material as possible.” The RADAN symbols are created by Technical Engineer Mark Haskell’s team in the office, then Martin takes the live job on the shop floor producing the nests for that day with whatever other parts are going through in the same material.
The twin pallet Salvagnini L1Xe was the first in the UK when it was installed at their 10,000 square foot Wiltshire manufacturing plant. Altex say they could find nothing to match its overall performance of cutting five times faster than the eight-year-old 3kw machine it replaced. They manufacture from different grades of steel along with titanium, tungsten, inconel, and aluminium including 1050A which the more conventional C02 lasers find difficult. “And the wavelength of the fibre laser means it can easily cut highly reflective materials such as brass and annealed copper – which is impossible with C02 lasers,” says Adrian.
‘Flexible’ and ‘dynamic’ are two words featuring strongly in the company’s vocabulary, which he says keep them ahead of the game in these difficult economic times, and are the reason he created Martin’s new nesting role a few months ago. Previously, nesting was handled in the engineering office and often meant producing nests well ahead of delivery dates. Standard nests were created, leading to a number of pre-lasered parts held in stock, and allowing remnants to build up.
“That has all changed with this new role,” says the MD. “It’s a very dynamic operation now, with Martin being right at the sharp end on the shop floor. He gets around 85% material usage, which, for some of the unusual shapes we cut, is extremely good. RADAN helps him use every piece of material he possibly can – if there’s space on a sheet, he’ll fill it.” This strategy has also helped reduce raw material stocks; Martin is also responsible for buying in the sheet material which he orders against the nests he has created. “We only buy the material we need.”
Mark says flexibility is another benefit of managing the RADAN nests on the shop floor. “Martin can control which nest he needs to run first. This is particularly valuable if we need to urgently laser parts for a specific job. Or in some cases remove these parts from the main scheduled nests and put them onto a separate offcut or sheet. The remaining scheduled nests can be re-nested very quickly without disrupting the running of the machine or reducing the sheet utilisation.”
The company, which celebrates its 30th anniversary in April, manufactures sheet metal products for a variety of industry sectors, including office furniture such as desks, screens, modesty panels, toolbars, paper trays and cabinets; components for commercial heating boiler systems; along with rollers and automated stackers used within the laundry industry. The Salvagnini also gives them the capability to produce the definition required for intricate titanium jewellery (pictured right)which they profile for a local Wiltshire based company.
Altex have developed a laser operation, punch operation and profile operation in RADAN’s e2i management system, giving Martin ease of control over whether a job is cut on the laser or punch press. “Some jobs are too intricate to punch, and we wouldn’t laser a job with hundreds of holes,” says the MD. “Also, some jobs would go on both machines; where there are intricate profiles we’ll form on the punch first, then bring the part over to the laser, and using its positional sensors to pick up on the holes and sheet edges we’d then cut around those.” Some larger panels would be lasered first, then put on the punch to produce extra holes.
Where bending is required, the parts are forwarded to their LVD and Bystronic press brakes driven by RADAN’s Radbend module. And Radbend provides Altex with a number of other “added value” aspects, as Mark explains: “When we undertake ‘Value Engineer’ projects for customers, the first option for cutting costs is to reduce the amount of welding. We use Radbend to see if it’s feasible to fold certain parts instead of welding.”
Where obscure folds are required on prototypes they are run through Radbend so the customer can be informed immediately if they are possible, and what the alternative folds or tooling would be.
“On batches of smaller folded parts we utilise a combination of RADAN’s improved common slit cutting feature and the Salvagnini’s cutting quality, to produce multi-fret parts for folding, which further increases sheet utilisation and reduces the profile time.”