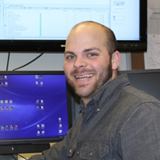
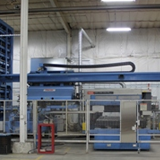
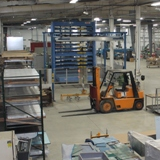
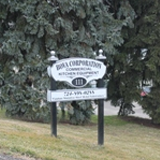
RADAN Macros Take Kitchen Company “To New Levels”
Two unique macros in the world’s most powerful sheet metal CAD/CAM software have improved a Pennsylvania commercial kitchen company’s abilities and taken them to new levels in processing and turnaround times.
The Bova Corporation produces sheet metal kitchens for organisations supplying food to the general public in places such as hospitals, hotels, schools and government departments. Head of Engineering Matt Bova (pictured right) says: “We do everything from basic wall shelves to full-blown serving lines incorporating the wiring and plumbing. We provide a turnkey operation for any aspect of kitchen ranges, mainly in stainless steel, with some components in galvanized steel and aluminum.”
They also manufacture laboratory equipment, stainless steel casework, counter tops and wall cabinets.
Typically, The Bova Corporation works from drawings provided by consultants and architects. “We take the plan view drawings and specifications of how the equipment should look, then lay out all the cabinetry and counter tops in Autodesk Inventor.”
Once the CAD is completed they are ready for CAM to prepare the parts for cutting on their Mazak Super Turbo X510 Hi-Pro laser (pictured left). And that’s where the market-leading RADAN CNC software comes in, with two macros written by the RADAN team especially for Bova.
The Inventor file is imported straight into RADAN using the first unique macro. It takes a Bill of Materials file from the kitchen drawing, putting all the parts directly into RADAN’s nest schedule editor. “This is invaluable to us because it dramatically reduces the time needed to process the parts from engineering to the shop floor. What was taking us two or three hours, now takes less than an hour.”
He says it also gives them confidence that everything will be 100% accurate. “Before the macro, human error meant we sometimes had issues with parts being skipped, quantities getting confused, and wrong materials and thicknesses. But now when I import CSV data into RADAN from Inventor a project file is automatically created, populating the nest schedule with all the parts in the Bill of Materials – materials, quantities and gauges.”
RADAN’s powerful nesting capabilities have improved Bova’s material utilization by around 25%. And a second macro written by the RADAN team kicks in at the nesting stage. Each nested part is given a label that prints out on a label maker, which Matt Bova says has helped them ten-fold. “Once the nests are created RADAN launches the label macro in Microsoft Word. Previously we had to write on each part with magic markers to label everything for assembly. Now we just peel the label off the sheet and stick it on the part. That’s helped us pick up more time.”
The simulation program is instrumental in preventing mistakes. “It shows that our cutting paths will be successful without us having to guess, taking away the need for trial and error and stopping material being wasted. This makes it invaluable for prototyping – and 95% of our work is bespoke so we do a lot of prototyping – as we can guarantee everything’s going to be right before we start cutting metal.”
Being able to program offline with RADAN means the laser is cutting one job while a CNC program is being produced for another one. “It keeps the machine operator busy at the same time as the programmer in the office.” And a staggered start means even more efficiencies: “Typically, a programmer will start an hour earlier than the operator, to RADAN all the parts and load up the laser with the parts that need to be cut. When the machine operator comes in everything’s ready for production to start, and the programmer moves on to the next job.”